Enhancing Predictive Maintenance & Operational Efficiency with Fiber Optic Hull Monitoring
Navigating the future with fiber optic sensing
Structural health & hull monitoring for the Maritime Sector
The maritime industry faces constant challenges in ensuring the safety, efficiency, and longevity of vessels and offshore structures. From the strong forces of the sea to the increasing demand for sustainable operations, the need for advanced monitoring solutions has never been greater. PhotonFirst is at the forefront of this evolution, providing cutting-edge fiber optic sensing (FOS) technology for maritime structural health and hull monitoring.
Our fiber optic sensing solutions offer real-time insights into the condition of critical maritime assets. By measuring strain, temperature, pressure, vibration, and acceleration, our systems provide a comprehensive understanding of structural behavior on your vessels. This enables proactive decision-making, enhances safety, and optimizes operational efficiency.
PhotonFirst collaborates with leading organizations in the maritime sector to develop and implement advanced FOS applications. We are committed to guiding and supporting our partners through every step, from initial concept and prototyping to testing, validation, and scaled-up operations using our unique PIC-based (Photonic Integrated Circuits) monitoring systems.
Why Fiber Optic Sensing (FOS) in vessels?
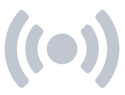
EMI-immune
Fiber optic sensors are inherently immune to EMI, ensuring accurate and reliable data in environments with strong electromagnetic fields from onboard electronic equipment.
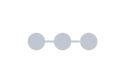
low footprint
A single fiber optic cable can measure multiple parameters (temperature, strain, vibration, pressure) at numerous points, simplifying installation and reducing cabling complexity.
-1.png?width=97&height=95&name=Icons%20all%20(1)-1.png)
COst effective & easier integration
The small size of fiber optic sensors facilitates easier and more cost-effective integration and installation.
.png?width=95&height=95&name=Accuracy%20%26%20reliability%20-%20PhotonFirst%20-%20Why%20(2).png)
High accuracy and reliability
Fiber optic sensors provide more precise and sensitive measurements compared to traditional strain gauges and electronic sensors.

durability in harsh environment
Our sensors and interrogators are inherently resistant to corrosion and are designed to withstand the challenges of the maritime environment, including exposure to saltwater, humidity, and extreme weather conditions.
Key applications of FOS in maritime
Hull Monitoring
Local and Global Stress Monitoring
Fiber optic sensors can be strategically placed on a ship's hull to measure the strain and stress experienced by the structure.
Local stress monitoring
Local stress monitoring focuses on specific areas of the hull that are prone to high stress concentrations, such as around welds, joints, or areas of potential impact. This helps in identifying and addressing localized weaknesses.
Global stress monitoring
Global stress monitoring provides a broader view of the overall stress distribution across the hull, helping to assess the impact of factors like weight distribution, cargo loading, and wave action on the vessel's structural integrity.
Local Load Monitoring
Fiber optic sensors can measure the forces and loads acting on specific parts of the hull. This is crucial for understanding how the hull responds to various operational conditions and external forces, such as those from waves or docking.
Slosh and Slam Impact Monitoring
Fiber optic sensors can monitor the impact forces and pressures resulting from sloshing and slamming, providing data to assess the potential for damage and improve hull design.
Sloshing
Sloshing refers to the movement of liquid cargo within tanks, which can exert significant forces on the tank walls and the hull structure.
Slamming
Slamming occurs when the ship's hull impacts the water surface with force, typically in rough seas.
Fatigue Damage Monitoring
Repeated stress cycles can lead to fatigue damage in the hull structure over time, potentially causing cracks and structural failure. Fiber optic sensors can continuously monitor strain variations, allowing for the detection and tracking of fatigue accumulation. This information is vital for predicting and preventing fatigue-related failures, ultimately extending the lifespan of the vessel.
Structural Temperature Monitoring
Temperature variations can induce thermal stresses in the hull structure, especially in extreme environments or in vessels carrying temperature-sensitive cargo. Fiber optic sensors can accurately measure temperature distributions across the hull, enabling the assessment of thermal stresses and their impact on structural integrity.
.png)
Monitoring of other critical assets
Commercial & Naval ships
Fiber optic sensing are well-suited for real-time remote predictive maintenance management and structural health monitoring of your fleet. Thanks to accurate and reliable data fleet operations can be optimized and reduced downtime can be achieved.
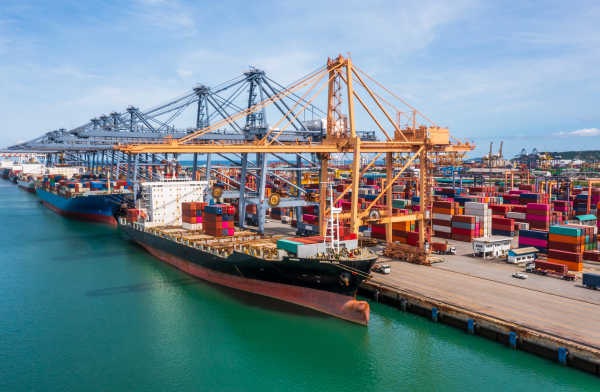
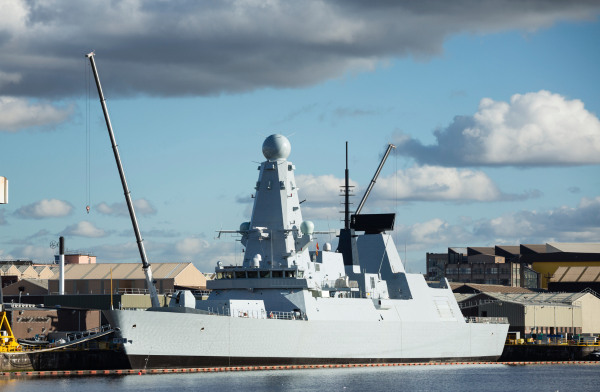
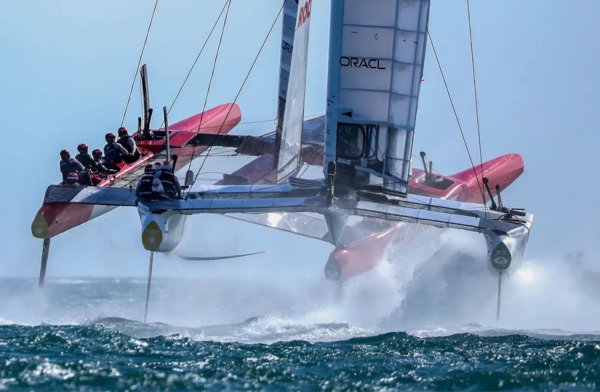
Sails & HYDROFOILS
Fiber optic sensors can be integrated into sails to monitor shape, strain, and stress distribution. This data can be used to optimize sail trim for maximum performance, detect potential damage, and improve sail design.
Hydrofoils are underwater wings that lift the hull of a vessel out of the water at high speeds, reducing drag and increasing performance. Fiber optic sensors can monitor the structural loads and deformations of hydrofoils, providing critical information for controlling and optimizing their performance and ensuring their structural integrity.
Offshore Structures
Offshore structures, such as oil platforms and wind turbine foundations, face harsh environmental conditions and complex loading scenarios. Fiber optic sensors can be used to monitor the structural health of these structures, detecting potential issues like corrosion, fatigue, and foundation settlement.
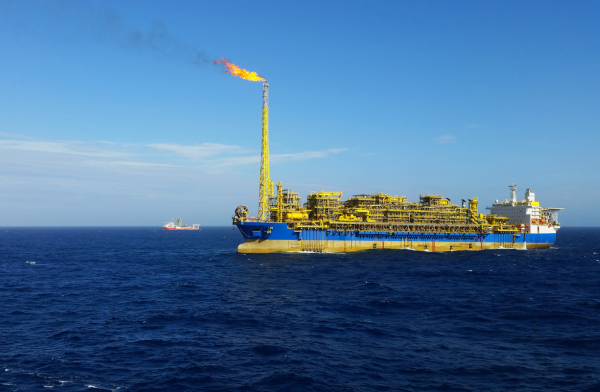
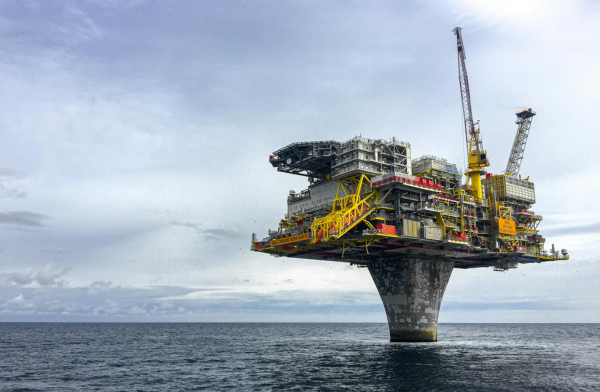
FPSO’s (Floating Production Storage and Offloading)
To run offshore oil and gas production and storage safely and efficiently, fiber optic sensors can monitor the hull integrity, mooring system loads, and riser integrity of FPSOs, ensuring safe and efficient operation.
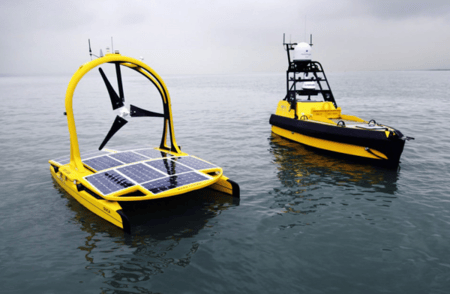
USV - Unmanned SURFACE Vehicle
Unmanned surface vessels, including autonomous ships and underwater vehicles, require reliable monitoring systems to ensure safe and efficient operation without human intervention. Fiber optic sensors are well-suited for these applications due to their small size, low weight, and ability to provide accurate data in challenging environments.
Use case
Project objective
- Improve predictive maintenance
- Extend operational lifetime
- Optimize design quality for new builds
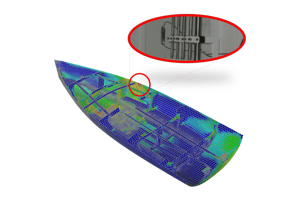
Solution
- Installation of multiple sensors and interrogators on 4 ships of DeVoogt
Achievements
- Monitoring of hogging, sagging, strain, vibrations and more, with FEA & FDA modelling of design for more than 2 years
- Structural behaviour analyses and validation of engineering models against actual wave and thermal loads
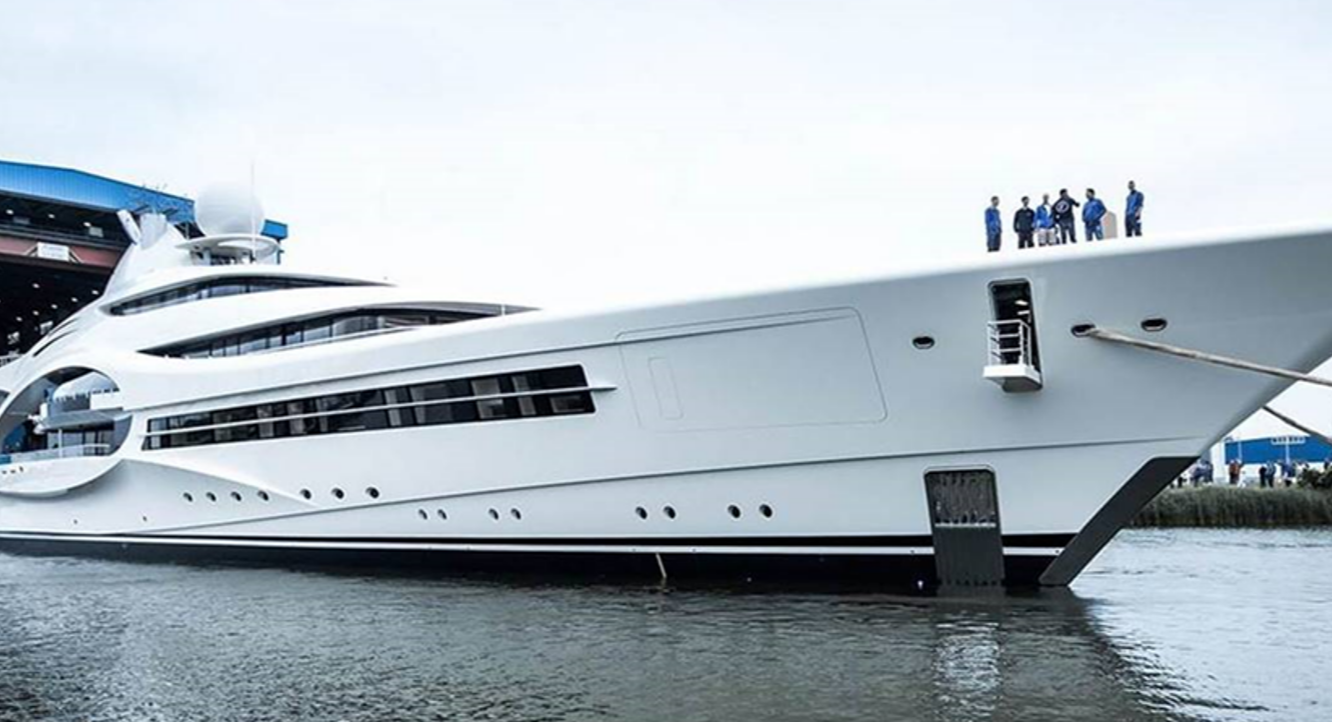
Source: De Voogt / Feadship